Woodworkers, carpenters, and DIY enthusiasts choose between many options when selecting the ideal finish for wood projects. Two of the most popular finishes include Danish oil and polyurethane. Both provide protective qualities to enhance the look and lifespan of wood pieces. However, Danish oil and polyurethane have distinct compositions, applications, and aesthetic effects.
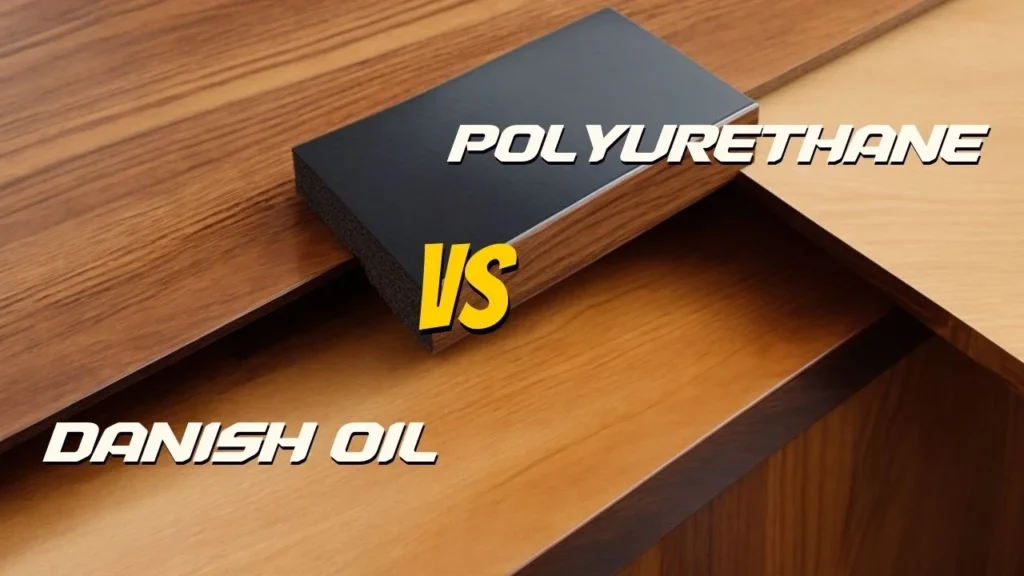
Understanding the key differences between these two finishes allows you to make the optimal choice for specific furniture pieces, wood characteristics, and project goals. Whether you seek to highlight the natural wood grain, desire maximum protection from scratches, or aim for an effortless application process, comparing Danish oil and polyurethane sheds light on their suitability.
Overview of Danish Oil and Polyurethane
Danish oil consists of a blend of oils and varnishes that penetrates wood pores to provide a protective, flexible coating that mildly amberizes over time. The key benefits of Danish oil include:
- Enhances wood grain by saturating pores while allowing texture to show through
- Easy wipe-on application that doesn’t require brush marks or many coats
- Provides a smooth, non-plastic feel compared to film-building finishes
- Accentuates depth and visual appeal, especially on lighter woods
- Available in natural and wood tone colors to influence coloration
- Easily applied to tight spaces like crevices and curves
- Repairs and touch-ups blend right in for inconspicuous fixes
Polyurethane is a synthetic resin-based finish that cures into a plastic-like coat on wood surfaces. Oil-modified polyurethane contains drying oils for better flow and leveling. The advantages of polyurethane include:
- Excellent moisture, scratch and chemical resistance to protect wood
- Highly durable coating for long-lasting finish
- Ultra smooth, glass-like surface when applied properly
- Crystal clear look showcases natural wood color
- Various sheens from matte to high-gloss
- Good flow and self-leveling properties
- Available as 1-part or 2-part catalyzed formulas
While both finishes protect and enhance wood’s appearance, their characteristics make each more suitable for certain uses. Understanding application methods, pros and cons will ensure you pick the best finish for your project’s needs.
Key Differences
Finish Feature | Danish Oil | Polyurethane |
Made of | Oil/varnish blend | Plastic resin |
Penetrates wood | Deeply | Minimal |
Protection level | Moderate | Maximum |
Moisture resistance | Medium | Excellent |
Sheen | Satin/low lustre | All ranges |
Toxicity | Moderate | High during application |
Food safe when cured | No | Water-based is |
Ambering over time | Low | Oil-based has slight |
Ease of touch up | Excellent | Difficult |
Texture retained | Excellent | Film can mask |
Cost | Low | Moderate |
Recommended Uses
Danish oil works beautifully on:
- Furniture – penetrates oak, walnut, teak pore structure for stylish sheen
- Wood doors, cabinets, trim – flexes seasonally without cracking
- Kitchen utensils, cutting boards, woodenware – accentuates figured grain patterns
- turnings, spindles, curved elements – effortless application
Polyurethane excels on:
- Tabletops – glass-like smoothness and stain resistance
- Flooring – tough durable plastic film withstands foot traffic
- High-use surfaces – kids’ furnishings, desks, countertops
- Outdoor furniture – moisture barrier protects against weathering
- Decor items – gloss poly highlights intricate details
On projects like professional bar tops or restaurant tables seeing extreme use, a poured epoxy resin finish often outperforms polyurethane for chip, scratch and heat resistance. But epoxy requires precise mixing and application to avoid drips, bubbles and yellowing over time.
Application Tips
To get the best results from Danish oil:
- Apply in a 65-80°F temperature range
- Allow proper drying times between coats
- Always wipe away surplus oil after 10-15 minutes penetration time
- Apply thin coats using a clean lint-free rag
- Sand lightly with 320 grit sandpaper before applying next coat
- Stop at 4-6 coat maximum to avoid gummy surfaces
- Use a maroon synthetic pad to gently buff each coat
- Work oil into endgrain thoroughly for even absorption
- Allow at least 7 days curing before subjecting to heavy use
For flawless polyurethane application:
- Only apply in dust-free room with over 60% humidity
- Ensure surface is free of wax, grease and sanding dust
- Use high-quality natural bristle brushes made for polyurethane
- Maintain a wet edge and move quickly to avoid lap marks
- Thin first coat 5-10% with mineral spirits for improved flow
- Apply thin coats, avoiding runs, drips or heavy buildup
- Lightly sand between coats to promote adhesion
- Allow 24 hours drying time minimum between coats
- Finish sand final coat to remove dust nibs and imperfections
- Allow 7+ days before heavy use for full curing
Composition and Key Characteristics
The Oils and Resins in Danish Oil
Danish oil contains a mixture of penetrating oils like tung and linseed oil combined with resins or varnishes. This blend absorbs deep into the pores of the wood rather than sit atop the surface. The oil components enhance the wood’s natural glow while the resins add a protective, hardened layer.
Compared to surface coatings like polyurethane, Danish oil allows more of the wood’s inherent texture, grains, and color variations to show through. The oils saturate deep within the wood grain to accentuate these organic qualities.
Since Danish oil soaks into the wood itself, it cannot peel or chip like surface coatings might when subjected to heavy use. The oils strengthen the wood fibers while the varnishes seal and protect the surface.
The Plastic Coating of Polyurethane
In contrast to penetrating oils, polyurethane forms a hard, plastic-like coating on the surface of the wood. This creates a smooth finish that encapsulates the wood beneath a durable film.
The polyurethane coating accentuates the shape of the wood rather than the grain. Depending on the brand and formula, polyurethane can impart a range of sheens from satin to high gloss. This consistency means polyurethane will have a similar effect across various wood species.
Polyurethane offers resilience against moisture, spills, scratches, and every day wear-and-tear. Its plastic-like barrier strengthens the wood surface to prevent dents and dings. However, the rigidity of the coating also means chipping and peeling can occur if the film becomes damaged.
Application Process: Danish Oil vs. Polyurethane
Effortless Application with Danish Oil
One of the key benefits of Danish oil is the ease of application. Prepping the wood surface is typically limited to light sanding before the first application.
Applying the oil simply involves wiping it generously onto the surface and across the grain. After 10-15 minutes, wipe off any excess oil with a clean cloth. Going with the wood grain helps remove surplus oil from the surface.
After 24 hours, a second thin application can enhance protection and richness. Danish oil penetrates efficiently into most wood species with this simple wiping method.
Challenging Polyurethane Application
Applying polyurethane requires careful prep and ideal environmental conditions. The surface must be free of any dust, oil or grease that could hinder smooth coating adhesion.
Polyurethane also demands a controlled application environment. Factors like humidity and temperature can impact cure time and the clarity of the finish. Cooler temps or high humidity prolong curing and drying.
Applying polyurethane with a brush risks leaving noticeable brush strokes. Spraying or wiping on thin coats creates a smooth, even look. Allowing sufficient drying time between coats prevents drips or tacky areas.
Despite the precise application process, polyurethane’s longevity and protective qualities make it worth the effort. Investing time in proper prep and application leads to a long-lasting, durable finish.
Maintenance and Durability Factors
Regular Reapplication Needed for Danish Oil
One downside of Danish oil’s penetration into the wood grain is the need for reapplication every year or two. Since the oils absorb into the wood itself, the finish gets replenished with regular re-oiling.
With heavy use, Danish oil may need reapplication every 1-2 years. This maintains the enriched color and protection against minor scratches, moisture rings, and stains. Danish oil cannot prevent deep gouges, but it disguises surface level imperfections well.
While Danish oil enhances water resistance, it does not waterproof the wood completely. Coaster use helps prevent moisture rings on tabletops.
Polyurethane’s Long-Lasting Protection
In contrast to Danish oil, polyurethane can easily last 5-10 years before needing a fresh coat. Its plastic-like barrier prevents not only scratches and dings, but also moisture damage. The thickness of the coating relates directly to its durability.
Polyurethane excels at protecting tabletops, desks, floors, and any high-use surfaces. Only deep gouges or cuts can penetrate through the tough coating. Spills and condensation wipe away easily without damaging the underlying wood.
The trade-off for polyurethane’s longevity is the intensive prep work needed before reapplying a fresh coat. You must sand away the previous finish completely to achieve proper adhesion.
Aesthetic Impact: Natural Wood vs. Consistent Finish
Danish Oil Accentuates the Wood’s Natural Beauty
For projects aimed at showcasing the natural wood grain, Danish oil provides the ideal enhancement. The oils magnify the depth and textures of the grain pattern. This allows unique characteristics of the wood like swirling grains or color variations to take center stage.
Danish oil is especially suitable for highlighting figured wood patterns like birds eye maple. The oil soak brings out the three-dimensional figuring while offering protection.
On open-grained woods like oak or mahogany, Danish oil emphasizes the dramatic pores and growth ring patterns. Using it on closed-grain woods like cherry or maple illuminates subtle grain details.
Polyurethane Offers a Uniform Finish
In contrast, polyurethane creates a smooth, consistent coating across wood species and surfaces. The plastic-like film minimizes the visibility of pores, grains, and natural imperfections.
While this provides durability for tabletops and high-traffic surfaces, it reduces the wood’s organic identity. The chief advantage of polyurethane lies in its reliable performance rather than enhancing wood character.
Polyurethane finishes range from a silky sheen to a thick glossy coat. The chosen sheen impacts the wood’s visibility—satin or matte polyurethanes allow more of the underlying wood to show through.
Combining the Two Finishes for the Best of Both Worlds
Rather than choosing exclusively between Danish oil and polyurethane, many woodworkers use both finishes in sequence.
The oil provides the initial protection and color enhancement while allowing the wood grain and texture to remain visible. Adding a layer of polyurethane over the Danish oil boosts the durability and scratch resistance.
This combined approach provides a natural, matte look from the oil along with the protective benefits of polyurethane. Applying coats of urethane with a wipe-on method helps maintain a smooth, flowing finish.
Proper drying times between the Danish oil, sanding, and polyurethane application prevent issues like tackiness or clouding. Patience creates an ideal melding of the two finishes.
Comparing Finnish and Use Cases
Danish Oil for Home Office Desks
For a home office desk likely to receive daily use but not extreme wear-and-tear, Danish oil provides sufficient protection. It allows the wood’s grain to remain visible while preventing minor scratches, stains, and rings from office work.
Reapplying a fresh coat of Danish oil every 1-2 years will maintain the finish. If heavy mug or cup use is expected, using coasters and a polyurethane topcoat offers extra protection.
Layering Polyurethane Over Danish Oil
Applying polyurethane over Danish oil combines the benefits of both finishes. The Danish oil maximizes the wood’s natural appearance while the polyurethane boosts durability.
Allow the oil to cure fully, applying a second coat if desired. Lightly sand the surface before applying thin coats of polyurethane. Limiting the coats to 2-3 prevents obscuring the wood grain
Using Danish Oil Before Polyurethane on Red Oak
For porous open-grained woods like red oak, pre-treating with Danish oil ensures adequate penetration before applying polyurethane. The oil soaks into the deep pores before the polyurethane forms its protective coat.
This prevents a porous, uneven look from polyurethane alone. The oil evens out the wood grain and enhances color richness. After the oil cures, wiping on 2-3 polyurethane coats provides a smooth, durable finish that still allows the wood’s character to show.
Evaluating Danish Oil’s Waterproofing Abilities
While Danish oil enhances moisture resistance, it does not completely waterproof wood. The resins in the oil formulation help repel water and prevent ring formation. However, prolonged moisture exposure will still damage the wood itself.
For surfaces like tabletops or bathroom vanities that see frequent spills, polyurethane or a combined Danish oil and polyurethane approach provides better protection. Using coasters helps prevent mug rings regardless of finish.
Exploring Alternatives Beyond Danish Oil
Tung oil offers more water resistance than Danish oil while enhancing the wood grain. Pure tung oil is food safe when fully cured making it ideal for cutting boards and butcher blocks. It richly accentuates figured wood patterns. Straight tung oil requires 7-10 days curing per coat.
Shellac brushes on easily to yield a lustrous finish with good moisture resistance. The natural resin varnish provides minimal grain enhancement but dries quickly for rapid project completion. Shellac sticks to almost any surface while allowing diverse stain, glaze and paint treatments on top. However it’s prone to water spotting and scratches.
Lacquer sprays on rapidly in thin coats to create a durable finish. It dries fast for quick handling and recoating. Brushing lacquer is also available. Lacquer exhibits good moisture, heat and chemical resistance while bringing out a crystal clear rubbed-out gloss. But spray fumes are flammable and harmful. Proper respirators are essential.
Wax offers a hand-rubbed luster and tactile feel. Wax is easy to apply but provides limited moisture barrier qualities. Regular renewal is needed for continued protection. Use over Danish oil or polyurethane reduces sheen while increasing surface slide. Wax effectively fills pores on open grained woods.
Oil and wax blends like Wood wax, OSMO Polyx and others fuse oil’s penetration with wax’s low sheen. These prove excellent on furniture while requiring more frequent renewal than Danish oil or polyurethane alone. Hard wax oils combine durability with a matte appearance.
What Surpasses Danish Oil for Protection?
For ultimate moisture protection and durability, marine spar varnish and epoxy resin offer stronger resistance than Danish oil. But neither enhances wood grain visibility like oil.
Using Danish oil first followed by coats of marine varnish combines aesthetics and protection. Epoxy resins create a plastic-like coating that fully encapsulates the wood.
Comparing Danish Oil and Traditional Varnish
While Danish oil contains varnish components, pure varnishes like polyurethane form a harder film coating versus soaking into the wood. This leads to a more uniform appearance and increased surface protection compared to Danish oil.
But varnishes can appear “plasticky” and obscure wood grain. Oils enhance texture and depth while allowing minor imperfections to show. The choice depends on the desired finish clarity and protection level.
Conclusion
Danish oil and polyurethane each offer distinct advantages as a woodworking finish. Oil provides a natural feel that enhances grain, while polyurethane creates a tougher protective barrier. Consider the end use and desired aesthetics when selecting between these two quality finish options. With proper application both can create durable, beautiful results. Test samples on scrap wood aid the decision process. Wood’s unique organic beauty deserves the ideal finish tailored to the project’s purpose.