Cherry wood holds a special place in fine woodworking and furniture making. Known for its distinctive red undertones and ability to mellow into a richer, darker color, cherry’s aging process is integral to its natural beauty. Unlike woods that maintain a relatively constant color, the changes that occur in cherry wood over the years are prized by woodworkers and collectors alike.
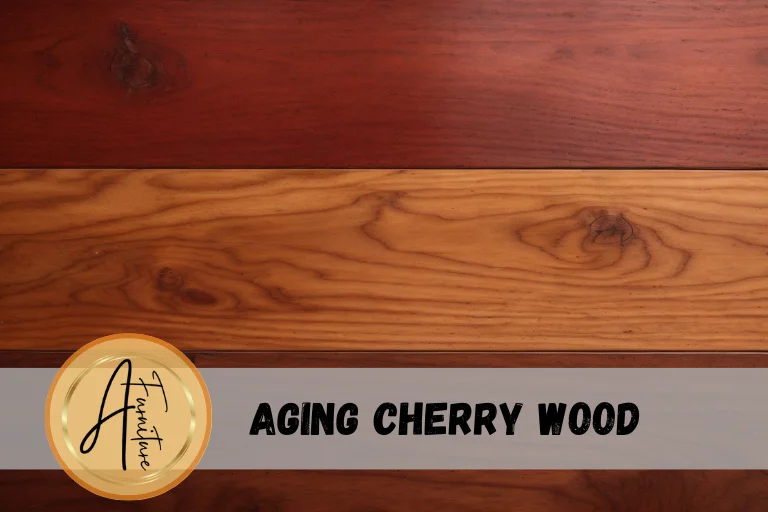
Understanding the science behind cherry wood’s aging process enables woodworkers to showcase this wood’s finest attributes better. It also allows furniture buyers to make informed decisions about cherry wood pieces, recognizing that the cherry wood of today will take on a different, more refined look in the future. From the factors that speed up or slow down the aging timeline to techniques for blending old and new cherry wood, this guide will explore the art and science of cherry wood’s mesmerizing maturation.
The Natural Aging Process of Cherry Wood
Cherry wood, particularly American cherry (Prunus serotina), starts with a light reddish-brown color when freshly cut and milled. Over months to years, oxidation and exposure to light cause the color to deepen into a richer, darker reddish-brown, sometimes taking on a slight plum hue. This color change occurs in both heartwood and sapwood, though heartwood tends to darken more.
Unlike pine, oak, and other woods that retain their blondish hue, cherry wood transforms dramatically. This process is primarily driven by oxidation and UV light exposure. As the wood’s cells are exposed to oxygen and sunlight, chemical changes occur. Key phenolic compounds in the wood – notably tannins – undergo oxidation reactions, forming new, darker pigments. The same chemical process causes freshly cut apples and avocados to darken.
Meanwhile, ultraviolet rays from sunlight break down lignin compounds in the wood, also facilitating darkening. Exposure to UV light speeds up the overall process significantly. The combination of oxidation reactions and UV exposure gives aged cherry wood its mature, refined look.
The Speed of Aging: Factors that Affect It
While cherry wood’s aging process occurs naturally over 1-3 years, several factors affect the rate and degree of color change:
Sunlight Exposure: Direct sunlight dramatically accelerates darkening, especially UV rays. Indoor cherry wood may take decades to reach its darkest mature color. But outdoor cherry wood in sunny environments can turn reddish-brown to dark reddish-brown within 1 year.
Wood Location: Heartwood near the tree’s center tends to darken more than sapwood on the outer edges. Figuring and grain patterns also impact oxidation rates. Burls, curls, and birdseye figuring tend to darken more rapidly.
Finish: Oil finishes allow more oxidation and UV penetration than film-building finishes like polyurethane. Unfinished wood ages fastest. However, a light stain helps counteract uneven blotchiness as cherry wood ages.
Environment: Dry, sunny climates speed up maturation. Increased humidity slows the loss of natural oils, while pollution may dull oxidation. High altitudes increase UV exposure. Coastal climates also age cherry wood rapidly.
Initial Color: Greener, less mature cherry cuts exhibit less reddish-brown pigments initially. But given the same conditions, they ultimately end up a similar rich color as wood cut from older trees.
With ideal conditions like full sun outdoors, the darkest “aged” cherry color can be attained in as little as 6 months. Witnessing significant darkening indoors with low light may take up to 10 years. Cherry wood’s aging pace is rapid compared to more stable woods like oak or walnut.
Chemical Aging: Quickening the Process
While natural aging takes patience, there are ways to quickly darken cherry wood for projects requiring an antique, aged look. Chemicals such as iron acetate, potassium dichromate, or sodium hydroxide (lye) can react with tannins in the wood to accelerate darkening. This chemical aging process provides deep color in days instead of years.
Iron Acetate is the most commonly used chemical for aging cherry. Applying iron acetate and allowing it to soak into the grain mimics years of natural oxidation. Typical dosage is 1-3 ounces dissolved in 1 quart of water. Multiple coats may be applied to reach the desired hue. Iron acetate doesn’t significantly raise the wood grain.
Potassium Dichromate works similarly to iron acetate but is more caustic and requires safety precautions. It tends to produce blotchier results. Lye (Sodium Hydroxide) also ages wood rapidly but drastically raises the grain, requiring sanding.
While chemical aging speeds the process, it lacks the nuanced, graceful color changes of natural aging. Pigments may appear slightly artificial. Uneven blotching is also more likely than the subtle variations of naturally aged cherry. But chemical aging can be an excellent solution for projects requiring a quick aged effect.
The Woodworker’s Perspective: Planning and Matching
Woodworkers who regularly work with cherry understand its tendency to color-shift over time. This aging behavior influences design and construction decisions. The initial reddish-brown color previews the deeper hue since a new cherry wood piece will gradually darken with age.
When making cherry furniture or cabinetry, anticipating this color change is key for achieving a cohesive look. One approach is selecting cherry wood with whiter sapwood to contrast against heartwood that will grow darker. Stains can also be used to even out colors for a uniform aged look. Joining methods are chosen to allow for wood movement as cherry matures.
Matching new wood to existing cherry is an art. First, scrutinize the existing wood color. Then select planks that are initially lighter but will deepen to that mature shade. Glancing at end grain reveals heartwood vs. sapwood proportions. Also examine color consistency and grain patterns. Once matched boards are found, suitable joinery and finishing methods can unify old and new elements.
Artisans can intentionally showcase aged and newer wood by understanding cherry’s aging tendencies. A mix of hues displays cherry’s full range. As the new wood color shifts, the initial mismatch steadily resolves into a well-planned, coordinated look. Patience and experience pays off handsomely.
Stains and Finishes: Impact on Aging
Stains and protective finishes also influence cherry’s aging process. Stains in particular help compensate for uneven pigmentation as cherry matures. The right combinations control color change while allowing the wood’s natural richness to emerge.
Light stains even out cherry wood’s color but allow plenty of aging. Thin, dilute dye or pigment stains add subtle tone while exposing the wood. Yellow, brown, and red shades harmonize with developing undertones. Light spray applications tint evenly. As cherry ages, its figure and grain remain visible.
Medium-toned stains provide more masking while permitting some aging. Fuller dyes and wiping stains give cherry a constant base color but don’t overpower the wood. Umber, chestnut, and mahogany hues work well. Heavier pigment concentrations ensure stability and hide splotchiness.
Dark stains dominate cherry’s natural color, creating bold effects. Since the wood’s undertones are obscured, uniformity and less aging is achieved. But with opaque stains, cherry’s beauty is displayed without showcasing its maturation.
Film finishes like polyurethane slow oxidation and UV effects significantly. The wood takes much longer to age, retaining a fresher look. Multiple coats severely hinder aging. But thinned varnishes only moderately impede maturation. Oils allow cherry to evolve naturally.
Balancing control versus natural character is key. With careful finishing, cherry’s alluring color variations can take the spotlight.
The Aesthetic Appeal of Aged Cherry Wood
Cherry’s rich patina and luster after decades of maturation is a prize worth waiting for. Like a fine wine, the wood’s warm, refined hues and smooth texture only improve with time. Parts of a tree cut years ago alongside newer planks will show obvious color differences, creating dynamic contrasts.
This aged beauty and shift from reddish-brown to deep reddish-brown is part of cherry’s intrigue. Unlike ash, maple, and other stable timbers, cherry wood visibly changes. At the same time, it maintains its familiar grain patterns, echoes of the living tree it once was. This tangible history and evidence of passing decades gives aged cherry wood vintage appeal.
The concept of patina in materials like bronze and wood is key. Patina refers to a surface’s lustrous, mellowed appearance after prolonged exposure and use. Just as antique furniture acquires a desirable sheen from generations of handling, cherry wood matures all on its own. Time’s passage only enhances its warmth and dignity. This patinated glow can’t be faked or rushed.
Cherry’s laid-back personality also shines through. Its predominantly straight, even grain exudes an easygoing character. Aged cherry beckons people to touch its smooth surface and appreciate the wood’s story. Blonde and lifeless when young, it transforms into an honored elder. For woodworkers, properly aged cherry represents a career’s accomplishments
Additional Tips and Tricks
Here are quick tips for guiding cherry wood’s aging process:
- Expose unfinished cherry wood to ample sunlight to accelerate natural aging.
- Apply light stains to minimize blotchiness yet allow some color development.
- Use oil finishes to maintain a protective barrier while permitting gradual oxidation.
- Avoid excessive humidity and over-drying to prevent distortion as wood ages.
- Add accents like ebony inlays that contrast with deepening cherry wood tones.
- Combine aged and unaged cherry boards to showcase the full color spectrum.
- Use shellac or varnish on select areas to purposefully inhibit aging.
Conclusion
Cherry wood’s distinctive aging process distinguishes it from more static woods prized for stability. Young cherry matures into a richer, more refined version through a fascinating interplay of chemical reactions and environmental factors. Both time and techniques exist to coax out cherry wood’s full potential.
This guide has illuminated what drives the change, from oxidation and UV rays to wood finishing choices. Whilecherry’s maturation can be accelerated, and traditional aging delivers the most authentic, nuanced hues and texture. Much like caring for an heirloom, cherry wood deserves patience.
For woodworkers, anticipating cherry’s color shift is key to creating harmonious designs that stand the test of time. The wood’s mellowed patina only increases its vintage appeal. Cherry combines durability with warmth and a laid-back, inviting spirit. Aged cherry wood satisfies visually and to the touch, wearing its history with quiet pride.